Thursday November 26, 2015 at 4:09pm
In this Blog post SOLIDWORKS Simulation has been coupled with the ‘Design Study’ tool to run a batch of static studies and optimise a quadcopter frame.
Quadcopters
are small unmanned aerial vehicles that use four vertical rotors for both
lifting and manoeuvring. Their simple design (no rotor articulation) made them
very attractive for model-making enthusiasts. However, they can carry only a
small electrical battery, which makes their flight time highly limited
(typically 10-20 minutes). Therefore, to increase endurance it is preferable to
have the frame structure as light as possible.
In
this case study SOLIDWORKS Simulation was coupled with ‘Design Study’ tool to
run a batch of static studies and optimise a quadcopter frame.
The frame created
for this study included all of the essential features: four rotor mounts and
beams, and a payload bay in the centre.


The
structure was modelled in a way that would allow to quickly alter the beam
thickness using a global variable.


A static
study was set up to simulate the worst case scenario of quadcopter climbing vertically
up with its highest achievable vertical acceleration. Assuming the craft would
be able to achieve its maximum rate of climb of 8m/s in 1 second – this was
evaluated to be 8m/s2.
The quad
copter mass was assumed to be 1.75 kg. ABS
PC material was applied to the model using SOLIDWORKS material database.
An FEA
configuration was made to use only a quarter of the model to speed up time to
solve. This was done using ‘Cut with Surface’ feature.

Symmetry
fixture was applied to sectioned faces and top face of payload bay was set to
fixed geometry.

The rotor
mount inner face was loaded vertically up as follows:
¼
of quadcopter mass X (Acceleration
due to gravity + Aircraft
acceleration) = 1.75 x 0.25 x (9.81 + 8) = 7.8 N

Design Study
(Evaluate>Design Study) was set up to simulate beam thicknesses between 1.00
mm and 2.00 mm with 0.05 mm step. The minimum factor of safety was set to 2 and
the goal of the study was to minimize mass.

Results:
After going
through 21 scenario the optimal rib thickness was found to be 1.8 mm resulting
in 41.74 g for the quarter model, or 167 grams for the whole frame.

Results were
also saved out in a .csv file to create a plot which illustrates how F.O.S
rises with increasing the beam thickness.

Conclusion:
With ‘Design
Study’ one can setup a batch of simulation jobs to help on choosing the optimal
structure that will satisfy the strength requirements
Rodion Radchenko
Applications Engineer
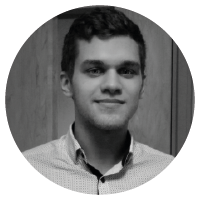